Scientists Uncover Why Foams Leak More Than Expected
Researchers at Tokyo Metropolitan University have unveiled groundbreaking insights into the long-debated phenomenon of foam drainage, challenging decades of established understanding in soft matter physics. Traditionally, the draining of liquid from foams was modeled by considering the foam as a static matrix of bubbles, with liquid trickling through the interstitial spaces governed primarily by osmotic […]

Researchers at Tokyo Metropolitan University have unveiled groundbreaking insights into the long-debated phenomenon of foam drainage, challenging decades of established understanding in soft matter physics. Traditionally, the draining of liquid from foams was modeled by considering the foam as a static matrix of bubbles, with liquid trickling through the interstitial spaces governed primarily by osmotic pressure—a factor related to bubble size and surface tension. However, these classical models tend to vastly overestimate the foam height necessary for liquid to begin draining from the bottom, often predicting heights far beyond what is observed in practical scenarios. The research team has now demonstrated that the onset of drainage is not dictated by static osmotic considerations but is fundamentally limited by the pressure required to cause bubbles within the foam to rearrange—a dynamic process governed by yield stress.
Foams are ubiquitous in everyday life, ranging from the cleaning foams employed in household products to the therapeutic foams used in pharmaceutical applications. Their complex structure comprises densely packed gas bubbles separated by thin liquid films, presenting a labyrinthine network through which liquid can migrate. The classical “absorptive limit” marks the threshold where liquid begins leaking out from the foam’s matrix. Prior models have assumed this threshold depends on osmotic pressure, which describes the energy alteration as bubbles deform and the contact area between gas and liquid changes under pressure. Yet, these models inefficiently capture real-world observations; liquid begins to drain from foams much shorter than the predicted heights.
The team led by Professor Rei Kurita approached this enigmatic discrepancy by devising a series of systematic experiments using surfactants to produce a diverse library of foams, each with distinct bubble sizes and liquid fractions. These foams were carefully placed between transparent plates and observed during the drainage process under upright conditions. Surprisingly, they discovered a robust universal scaling: the foam height at which drainage initiates is inversely proportional to the foam’s liquid fraction. This relationship held true irrespective of the surfactant type or the size of the bubbles, signifying that microscopic chemical and physical variations play a less dominant role than previously thought.
A critical breakthrough came when the researchers introduced the concept of an “effective osmotic pressure,” a parameter they derived by analyzing drainage limits across the foams tested. This effective pressure was markedly lower than what classical osmotic models predicted, suggesting another physical mechanism constrains drainage onset. To probe this, the team deployed high-resolution video microscopy to capture the dynamic processes inside foams at the critical drainage height. Contrary to the earlier belief that liquid simply flows through a rigid network of static bubbles, the footage revealed that liquid drainage coincides with noticeable rearrangement of bubbles themselves.
This dynamic rearrangement implies that foams exhibit a form of yield stress—a threshold stress below which the microstructure remains static, and above which the bubble network undergoes reconfiguration. Hence, drainage is not limited by the maximum osmotic pressure but by the minimum pressure necessary to overcome this yield stress and enable bubble motion. This insight transforms the way foam drainage is understood, from a static picture emphasizing fluid flow through fixed pathways to a kinetic framework in which the deformability and mobility of bubbles critically influence liquid transport.
The implications of this research extend beyond mere academic curiosity. It now becomes essential to factor in the rheological properties of foams when designing products that leverage foam stability and drainage behaviors. For example, in industrial cleaning agents or firefighting foams, optimizing the resistance to unwanted liquid drainage can enhance efficacy, while pharmaceutical foams might benefit from controlled drainage profiles for better delivery of active ingredients.
Furthermore, the study’s approach to correlating yield stress with drainage height provides a predictive tool that aligns closely with real-world foam behavior, resolving long-standing discrepancies in foam physics. This tool may inform future materials design, where tuning surfactant combinations and bubble sizes alone will no longer suffice without considering the mechanical stability and rearrangement thresholds of the foam network.
By repositioning foam drainage as a dynamic rather than a static phenomenon, the research opens new avenues for understanding soft materials more broadly. Soft matter physics, encompassing colloids, emulsions, and gels, often encounters systems where microstructural rearrangements govern macroscale properties. This study demonstrates how addressing these kinetic barriers fundamentally changes how such systems can be modeled and ultimately controlled.
The team’s innovative methodology, combining experimental observation with theoretical re-interpretation, highlights the importance of coupling solution dynamics with bubble kinematics—a previously underappreciated perspective in foam studies. This kinematic coupling lays the groundwork for more sophisticated models of sorption, drainage, and mechanical stability in complex fluid systems.
Funded by the Japan Society for the Promotion of Science (JSPS) KAKENHI Grant Number 20H01874, this research represents a significant leap forward in the physics of foams and soft matter. The findings are expected to influence future studies on multiphase materials and drive improvements in a myriad of commercial applications that depend on foam behavior.
As foams continue to play pivotal roles in consumer products, energy systems, and biomedicine, understanding such fundamental physical limits as revealed by Professor Kurita’s team will become increasingly vital. The elegant combination of experimental precision and theoretical insight epitomizes the kind of multidisciplinary approach required to untangle the complex dynamics seen in everyday but scientifically rich materials like foams.
In summary, this pioneering research from Tokyo Metropolitan University fundamentally redefines foam drainage by demonstrating the central role of yield stress-induced bubble rearrangements. This dynamic mechanism accounts for why practical foams drain at heights far below those predicted by static osmotic pressure models. The breakthrough shifts scientific paradigms around soft materials and opens novel practical avenues for engineering foams with tailored drainage properties.
Subject of Research: Understanding the mechanisms governing liquid drainage from foams.
Article Title: Absorptive limits of foams governed by kinematic coupling between solution and bubbles
News Publication Date: 5-May-2025
Web References: DOI: 10.1016/j.jcis.2025.137746
Image Credits: Tokyo Metropolitan University
Keywords
Foam physics, Soaps, Osmotic pressure, Soft matter, Emulsions, Surfactants, Microfluidics
Tags: bubble rearrangement pressureclassical models of foam behaviorcleaning foams in household productsfoam drainage dynamicsinsights into foam leak phenomenainterstitial spaces in foam structureliquid migration in foamsosmotic pressure in foamspractical applications of foamssoft matter physics advancementstherapeutic foams in pharmaceuticalsyield stress in foam stability
What's Your Reaction?
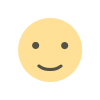
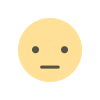
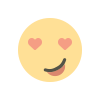
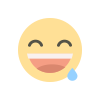
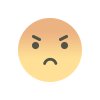
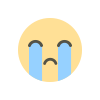
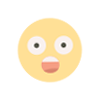