Revolutionizing Resource Independence: The Rise of Domestic High-Performance Permanent Magnets!
The Nano Materials Research Division at the Korea Institute of Materials Science (KIMS) has reached a pivotal milestone in the field of magnet production with the introduction of an innovative grain boundary diffusion process. Spearheaded by researchers Dr. Tae-Hoon Kim and Dr. Jung-Goo Lee, this cutting-edge technology has the potential to transform the landscape of […]

The Nano Materials Research Division at the Korea Institute of Materials Science (KIMS) has reached a pivotal milestone in the field of magnet production with the introduction of an innovative grain boundary diffusion process. Spearheaded by researchers Dr. Tae-Hoon Kim and Dr. Jung-Goo Lee, this cutting-edge technology has the potential to transform the landscape of permanent magnet synthesis, paving the way for high-performance magnets free from heavy rare earth elements. This achievement is particularly significant given the ongoing global reliance on these rare materials, which are primarily sourced from China.
Permanent magnets are ubiquitous in modern technology, serving as critical components in high-value products such as electric vehicle (EV) motors, robotics, and various consumer electronics. The conventional methods of manufacturing permanent magnets have depended heavily on heavy rare earth elements, a scenario that has perpetuated significant resource vulnerabilities. With a monopoly on these materials, China’s dominance leads to not only inflated production costs but also geopolitical concerns over supply security. This scenario has prompted researchers and industries worldwide to cultivate alternative strategies that do not hinge on these rare and expensive resources.
The crux of KIMS’s groundbreaking technique lies in a two-step grain boundary diffusion process, a method designed to augment the magnetic performance of permanent magnets. In this process, the magnet’s surface is initially coated with heavy rare-earth materials, followed by a thorough high-temperature heat treatment. During this crucial phase, these rare elements diffuse into the magnet’s interior, navigating along the grain boundaries, which serves to enhance coercivity—the magnet’s ability to maintain its magnetization over time.
In budding innovation, the research team at KIMS has meticulously engineered a unique two-step protocol that begins with the thermal infiltration of a specially formulated high-melting-point metal into the magnet at elevated temperatures. This initial stage aims to set a robust foundation for optimal magnetic properties. Following the high-temperature procedure, the magnets undergo room-temperature cooling, which prepares them for the subsequent step. In the second phase, a low-cost light rare earth, specifically Praseodymium, is reintroduced into the magnet at high temperatures. The inventive aspect of this approach lies in its ability to prevent abnormal grain coarsening during the diffusion process. This phenomenon has previously hindered the efficiency of conventional grain boundary diffusion methods, resulting in diminished magnet performance. The KIMS team has successfully developed techniques to manage this issue, significantly boosting diffusion efficiency.
What distinguishes this new method is its rapid infiltration of diffusion materials into the magnet, which not only improves magnetic coercivity but also allows the resultant product to achieve coercivity grades between 45SH to 40UH. Remarkably, this performance benchmarks it alongside commercially available magnets that utilize heavy rare earth elements, despite the absence of such costly materials in the manufacturing process.
The implications of this advancement extend far beyond mere performance metrics. If successfully commercialized, this new technology promises dramatic reductions in manufacturing costs, alongside enhanced performance for critical applications in high-value industries that require efficient motors, including electric vehicles, drones, and futuristic flying cars. As the demand for sustainable and economically viable alternatives increases, KIMS’s innovation stands to disrupt not only existing supply chains but also influence research trajectories across the globe.
Dr. Tae-Hoon Kim, the principal investigator in this transformational study, elaborated on the broader significance of their work. He emphasized the inherent challenges posed by the reliance on costly heavy rare earth elements, particularly for electric vehicle motors and premium home appliances. He noted the geographic concentration of these resources and their associated costs, which have spurred extensive research efforts worldwide to identify alternatives. Until now, progress in this arena had been stymied, but this breakthrough offers a promising pivot point.
The advent of this novel grain boundary diffusion process signals a new direction not just for KIMS or South Korea, but for the global magnet manufacturing industry. It illustrates the potential to move away from the traditional dependency on rare earth elements, a shift that could establish new paradigms for future research directions in grain boundary diffusion processes. Kim firmly believes that with successful commercialization, this could herald South Korea’s emergence as a leader in a field critical to various technological innovations, damaging the monopoly that other nations, particularly China, have held for so long.
The research effort has received robust backing from the Ministry of Science and ICT as well as the National Research Foundation of Korea under the Nano and Materials Technology Development Program. The outcomes of this study have recently been published in the prestigious journal Acta Materialia, signaling the study’s recognition within the scientific community.
Overall, the grain boundary diffusion process represents a landmark achievement not just for KIMS but for the advancement of materials science as a whole. As further inquiries and developments stem from this research, the implications for industry and technology are boundless.
The commitment to advancing sustainable and cost-effective manufacturing practices reflects a growing consciousness within the scientific community about the essentiality of responsible resource use. The KIMS team’s work showcases the paradigm shifts possible when innovation and research dedication align, centering on the objective of breaking free from the limitations imposed by current resource dependencies.
Subject of Research: Grain Boundary Diffusion Process for Permanent Magnets
Article Title: A novel two-step grain boundary diffusion process using TaF5 and Pr70Cu15Al10Ga5 for realizing high-coercivity in Nd-Fe-B-sintered magnets without use of heavy rare-earth
News Publication Date: 24-Dec-2024
Web References: http://dx.doi.org/10.1016/j.actamat.2024.120660
References: Acta Materialia
Image Credits: Korea Institute of Materials Science (KIMS)
Keywords
High-performance magnets, grain boundary diffusion process, rare earth elements, KIMS, electric vehicles, coercivity.
Tags: advancements in materials sciencealternative strategies for magnet sourcingdomestic magnet production technologyelectric vehicle motor componentsgeopolitical implications of magnet supplygrain boundary diffusion processhigh-performance permanent magnetsinnovations in magnet manufacturingKorea Institute of Materials Science researchreducing reliance on rare earth elementsresource independence in technologysustainable magnet synthesis methods
What's Your Reaction?
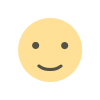
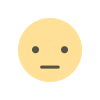
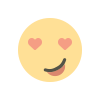
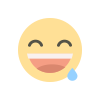
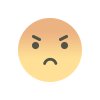
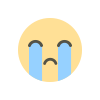
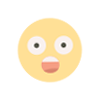