Revolutionary Fabrication Technique Powers Up Artificial Muscles
Researchers at The University of Texas at Dallas have recently unveiled an innovative and cost-effective methodology for the creation of artificial muscles, a breakthrough that could have significant implications across various fields, including robotics and adaptive wearables. This advanced technique promises to enable the development of robots equipped with highly efficient movement capabilities and clothing […]

Researchers at The University of Texas at Dallas have recently unveiled an innovative and cost-effective methodology for the creation of artificial muscles, a breakthrough that could have significant implications across various fields, including robotics and adaptive wearables. This advanced technique promises to enable the development of robots equipped with highly efficient movement capabilities and clothing that can intelligently respond to environmental temperature changes, enhancing comfort for the wearer. Such advancements, derived from the new fabrication method, are set to reshape our understanding of material applications in both technological and everyday contexts.
The research findings were published in the prestigious journal Science on March 7, where the team detailed their mandrel-free fabrication system for constructing polymer-based artificial muscles with remarkable properties. Notably, these new muscles can stretch up to 97% of their original length and possess a spring index exceeding 50. The spring index is a critical measurement in the realm of synthetic muscle design, reflecting the relationship between the coil’s average diameter and its constituent fibers or wires. Lower spring indexes signal a more tightly wound, stiffer muscle, whereas higher indexes correspond to looser coils that are more flexible, reminiscent of children’s toys like Slinky.
Dr. Ray Baughman, who helms the Alan G. MacDiarmid NanoTech Institute at UT Dallas, leads this pioneering research. Baughman is a recognized figure in the field of artificial muscle technology, with previous work exploring the potential of various materials, including coiled fibers and carbon nanotubes. Historically, the coiling of fibers around a mandrel—a spindle used to shape the material—was the standard practice for creating these muscles. This method, however, was not without downsides; it often resulted in material waste and higher production costs because the mandrel was discarded following the process, which utilized a large-diameter polymer fiber.
Emphasizing the benefits of the new approach, Baughman articulated the challenges posed by the prior techniques. “The absence of comprehensive process reports detailing the production of mandrel-free, high-spring-index yarns has been limiting,” he explained. “Most approaches have relied on dissolving the mandrel after muscle formation. This creates unnecessary waste streams and undermines the economic viability of producing such advanced materials at scale.” The mandrel-free process not only sidesteps these issues; it also reduces fabrication costs, making it much more accessible for commercial applications.
Leading the charge on the development of this novel technique, Dr. Mengmeng Zhang, a research scientist at the NanoTech Institute, shared insights on how the technology could impact consumer products. “The mandrel-free method allows for high-spring-index yarns to be produced at a fraction of the previous cost,” Zhang noted. “This results in artificial muscles that can contract and elongate significantly based on temperature fluctuations, providing innovative solutions in adaptive wearables.” With these capabilities, jackets made from this technology could autonomously open and close thermal pores to maintain warmth as environmental conditions shift.
Revisiting previous endeavors, the research group had licensed its initial technology—crafted through the mandrel-wrapped process—to a clothing manufacturer that integrated the synthetic muscles into jackets worn by the U.S. team at the 2022 Winter Olympics in Beijing. However, the high production costs associated with that method hindered wider commercialization. Baughman pointed out that, with the introduction of the mandrel-free method, the potential for developing effective comfort-adjusting jackets within market reach has significantly improved.
Beyond clothing, Baughman and his collaborators have explored the diverse applications of their artificial muscle technology. The new manufacturing process affords variations in spring index along the muscle’s length, allowing for greater customization based on specific performance needs. This flexibility opens doors to numerous applications, including mechanical energy harvesting technology and self-powered strain sensors, particularly with the use of carbon nanotube yarns produced using the same mandrel-free fabrication technique.
The precise mechanisms driving the expansion and contraction of these artificial muscles are thermally activated, with heat introduced through electrical current, solvents, or electrochemical stimuli. This multifaceted approach to actuation enhances their utility in real-world applications, where environmental factors or user input can dictate the required muscular response.
In the fabrication process, the researchers employ a unique method wherein they impart twist into individual polymer fibers. This twist is precisely managed, ensuring that it does not exceed the threshold where the fibers would coil back on themselves. Subsequently, the twisted fibers are plied together, forming the spring-like coils. Each fiber acts as a mandrel for the other fibers, allowing them to form coiled structures without the need for an external spindle, thus significantly enhancing production efficiency.
The team has since filed a patent application for their new technology, underscoring their commitment to protecting this innovative advancement in material science. Funding for this groundbreaking research was generously provided by the Office of Naval Research, the Air Force Office of Scientific Research, and The Welch Foundation, highlighting the interest and importance of this work to national defense and technology.
In conclusion, the research conducted at The University of Texas at Dallas marks a significant paradigm shift in the field of synthetic muscle development. This new fabrication technique, being more cost-effective and environmentally friendly than its predecessors, is poised to enable a new generation of intelligent materials that can adapt to their surroundings in real-time. From robotics to fashion, the implications of these artificial muscles could revolutionize industries, presenting numerous opportunities for innovation and enhanced consumer experiences.
Subject of Research: Artificial muscles
Article Title: Mandrel-free fabrication of giant spring-index and stroke muscles for diverse applications
News Publication Date: 7-Mar-2025
Web References: DOI
References: Science journal
Image Credits: UT Dallas
Keywords
Artificial muscles, robotics, energy harvesting, polymer engineering, textile engineering, carbon nanotube fibers.
Tags: adaptive wearable technologyartificial muscle fabrication techniquesbreakthroughs in material applicationscost-effective muscle designDr. Ray Baughman research findingsimplications for robotics and wearablesinnovative manufacturing methodspolymer-based artificial musclesrobotics movement advancementsspring index in synthetic musclestemperature-responsive clothingUniversity of Texas at Dallas research
What's Your Reaction?
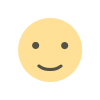
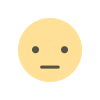
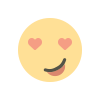
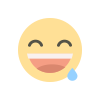
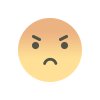
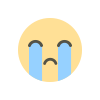
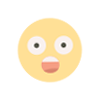