Robotic Automation Advances 2D Material Processing
The realm of two-dimensional (2D) materials has long held promise for revolutionizing the landscape of electronics and photonics, offering unprecedented opportunities for device miniaturization and performance enhancement. Among these ultrathin materials, graphene and related 2D crystals have attracted intense interest due to their extraordinary electrical, optical, and mechanical properties. However, a crucial bottleneck hindering their […]

The realm of two-dimensional (2D) materials has long held promise for revolutionizing the landscape of electronics and photonics, offering unprecedented opportunities for device miniaturization and performance enhancement. Among these ultrathin materials, graphene and related 2D crystals have attracted intense interest due to their extraordinary electrical, optical, and mechanical properties. However, a crucial bottleneck hindering their wide-scale application remains the transfer process—relocating these atomically thin films from their original growth substrates to target platforms required for next-generation technologies. In a groundbreaking advance, researchers Zhao, Liao, Bu, and colleagues have unveiled an automated robotic system that not only streamlines this transfer but also scales it to industrial levels, promising to accelerate commercialization and research of 2D materials significantly.
Chemical vapor deposition (CVD) stands as the most effective method to synthesize large-area, high-quality 2D materials suitable for industrial applications. Despite this, transferring the delicate, one-atom-thick films grown on metallic or other growth substrates to insulating substrates or device surfaces has been a manual and intricate task fraught with challenges. Traditional manual transfer processes suffer from low throughput, inconsistent material quality, frequent mechanical damages, and contamination risks that severely impede reproducibility and mass production. The novel automated transfer system reported by Zhao et al. tackles these issues head-on, employing robotics to manipulate and transfer the materials precisely while ingeniously engineering the interfacial adhesion and strain between layers to maintain integrity and quality.
This new system marks a paradigm shift by integrating automated handling with advanced interface science, thus addressing both the mechanical and chemical aspects of 2D material transfer. The researchers designed the robotic platform to carefully modulate the adhesion forces at the interface between the growth substrate and the 2D material during pickup, transfer, and deposition, ensuring minimal strain and preventing tears or wrinkles. This delicate balance of forces allows the atomically thin sheets to remain pristine, retaining intrinsic properties critical for device performance. Through these innovations, the system achieves transfer with graphene carrier mobilities surpassing 14,000 cm²V⁻¹s⁻¹, a metric indicative of near-ideal electrical conductivity and a hallmark of preserved material quality.
Beyond quality, the scale and consistency define this breakthrough. The authors demonstrate that their robotic approach can process up to 180 wafers per day, an industrially relevant throughput that dwarf conventional manual methods. Such volume is pivotal for integration into semiconductor manufacturing lines and for enabling the high-volume production of flexible electronics, sensors, and photonic devices built from 2D materials. The uniformity and repeatability achieved by the automated system significantly reduce device-to-device variability, facilitating reliable large-area applications and lowering barriers to market entry.
Cost and environmental sustainability often remain overlooked in pioneering fabrication techniques, yet Zhao and colleagues have addressed these dimensions pragmatically. Their automated transfer system decreases the dependence on costly consumables and labor-intensive procedures characterizing manual transfers. Additionally, the process minimizes chemical waste and lowers energy consumption, directly addressing environmental impact concerns pertinent to industrial-scale production. The environmental footprint reduction dovetails with cost savings to position this technology as not only state-of-the-art but also commercially viable and eco-conscious.
Zooming into the technical underpinnings, the automated system features a suite of robotic arms equipped with high-precision sensors and machine vision technologies. These tools monitor the transfer process in real-time, adapting the applied mechanical forces and timing to accommodate variability in substrate surfaces and 2D material properties. The programmed control algorithms leverage feedback from the sensors to fine-tune the adhesion-modulating parameters dynamically, ensuring that each transferred layer is free from mechanical defects like cracks, ripples, or contamination. Such integration of robotics and interface engineering exemplifies the move toward Industry 4.0 paradigms in material science.
The interplay of strain engineering is especially crucial given that mechanical deformation can introduce electronic disorder detrimental to the performance of 2D materials. Zhao et al. employed precise strain relaxation techniques within their robotic transfer protocol to maintain flatness and homogeneity, thereby conserving the atomic lattice order. This level of control is essential for applications such as high-frequency transistors, quantum devices, and optoelectronic components where even minor imperfections degrade function. By automating this process, the system ensures each wafer experiences consistent strain conditions, enhancing device reproducibility across production batches.
Moreover, the system’s ability to transfer various 2D materials extends its applicability beyond graphene. Transition metal dichalcogenides (TMDs), hexagonal boron nitride, and other emerging 2D semiconductors can benefit from this robotic method. These materials have distinct adhesion characteristics and strain sensitivities, yet the adaptable architecture of the platform allows easy tuning of transfer parameters to accommodate diverse materials. This versatility paves the way for fabricating heterostructures—combinations of different 2D layers with tailored electronic and optical properties—that are foundational to novel device architectures.
Notably, the researchers benchmarked their automated transfer results against conventional manual processes, revealing significant performance gains. Manual transfers often introduce contaminants, uneven adhesion, and physical damages, leading to poorer electronic properties and lower yields. In stark contrast, the robotic system consistently transferred graphene films with higher carrier mobilities and minimal defects, underscoring the effectiveness of robotics combined with interface control in producing high-quality 2D materials at scale. Such data will likely catalyze adoption by the semiconductor and flexible electronics industries.
Looking forward, this automated transfer platform could directly impact the commercialization timeline of 2D materials, which have lingered as promising yet elusive components in advanced electronics. The ability to process large quantities of defect-free materials reliably meets a critical industry requirement, enabling companies to design and produce 2D-based devices with confidence in supply chain quality and scalability. Furthermore, the reduction of human labor and error streamlines manufacturing workflows, contributing to lower costs and faster innovation cycles.
In parallel with commercial gains, this development has profound implications for academic and industrial research. High-throughput, low-cost access to uniformly transferred 2D materials will accelerate experimental exploration, from fundamental physics to new device prototypes. Having a widely available, automated method reduces the variability that hampered collaborative studies and data comparison across research groups. Consequently, this technology can help bridge the gap between laboratory-scale discovery and market-ready technologies.
Strategically, this breakthrough aligns with global efforts to integrate 2D materials into complementary metal-oxide-semiconductor (CMOS) technologies and flexible electronics platforms. The transfer process, historically a fragile and inconsistent step, can now be executed with reliability matching mature silicon fabrication processes. This bolsters the feasibility of hybrid devices combining 2D layers with silicon circuits, potentially unlocking new functionalities such as tunable photodetection, ultra-sensitive sensors, and energy-efficient logic components.
In terms of environmental stewardship, the researchers’ emphasis on reducing chemical consumption and process waste embodies best practices for sustainable nanomanufacturing. By automating transfer steps and using fewer reagents, they address significant hurdles that previously limited the ecological viability of 2D material production. This contribution is vital for ensuring that the scaling of advanced materials does not come at unacceptable environmental costs, a concern increasingly prioritized in high-tech manufacturing.
From a workflow perspective, integrating the automated system into existing manufacturing lines appears feasible, thanks to its modular design and compatibility with industry standards. This flexibility allows the robotic transfer technology to complement and enhance current CVD systems, creating a seamless end-to-end production pipeline. Such integration can shorten product development cycles and facilitate rapid scaling once device designs are finalized.
In summary, the automated robotic transfer system developed by Zhao, Liao, Bu, et al. represents a major leap forward in the fabrication of 2D material-based technologies. By ingeniously combining robotics, interfacial adhesion control, and strain engineering within a scalable platform, the system provides high-quality, uniform, and large-scale transfer capabilities previously unattainable. This innovation not only surpasses manual methods in throughput and quality but also aligns with cost reductions and sustainability goals. As a consequence, the present advance holds the potential to catapult 2D materials from research curiosities to mainstream components central to the future electronics and photonics industries.
Subject of Research: Automated robotic transfer of chemical vapor deposition-grown two-dimensional materials
Article Title: Automated processing and transfer of two-dimensional materials with robotics
Article References:
Zhao, Y., Liao, J., Bu, S. et al. Automated processing and transfer of two-dimensional materials with robotics. Nat Chem Eng 2, 296–308 (2025). https://doi.org/10.1038/s44286-025-00227-5
Image Credits: AI Generated
DOI: https://doi.org/10.1038/s44286-025-00227-5
Tags: advancements in 2D materials technologyautomated systems for material transferchemical vapor deposition for 2D materialsenhancing device performance with 2D materialsgraphene transfer challengeshigh-quality 2D crystals synthesisimproving throughput in material processingindustrial applications of 2D materialsmechanical properties of 2D materialsminimizing contamination in material transferrobotic automation in material processingscaling 2D materials for commercialization
What's Your Reaction?
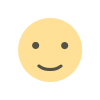
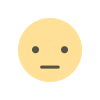
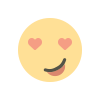
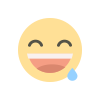
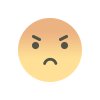
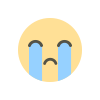
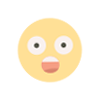