Revolutionary 3D-Printing Formula by Researchers Set to Redefine Foam Technology
Researchers at The University of Texas at Dallas have embarked on a groundbreaking journey into the world of materials science with their recent development of an innovative 3D-printed foam. This novel approach combines advancements in chemistry and technology, resulting in a product that promises to outshine traditional polymer foams in terms of both durability and […]

Researchers at The University of Texas at Dallas have embarked on a groundbreaking journey into the world of materials science with their recent development of an innovative 3D-printed foam. This novel approach combines advancements in chemistry and technology, resulting in a product that promises to outshine traditional polymer foams in terms of both durability and recyclability. Published in the March 1, 2025, issue of RSC Applied Polymers, the researchers have opened up new avenues for creating products that are both environmentally friendly and functional.
The appeal of this research lies not only in its potential applications but also in its scientific complexity. The journey towards creating this foam involved meticulously adjusting polymer formulations to ensure compatibility with 3D printing technologies. Co-lead author and doctoral student Rebecca Johnson shared insights into the challenges faced during the project, which spanned over two years. Achieving the right balance in the formulation was a painstaking process, but it ultimately led to a foam that can be manufactured effectively using 3D printing.
3D printing offers remarkable flexibility and customization capabilities that traditional manufacturing processes often lack. The researchers capitalized on these advantages by creating custom designs, such as a playful balloon dog figure, to demonstrate the foam’s potential. This combination of strength and lightness has significant implications for a range of industries, from packaging to automotive, where unique shapes and reliable insulation properties are highly valued.
In terms of practical usage, Dr. Ron Smaldone, the study’s corresponding author and associate professor of Chemistry and Biochemistry, emphasized the importance of addressing the limitations associated with current 3D printing technologies for foam manufacturing. He argued that there is a substantial need for materials that can serve both insulation and shock absorption purposes. As industries continue to seek innovative solutions for safety and efficiency, the dynamic properties of this foam could play a critical role in enhancing product safety.
One of the most intriguing aspects of the foam developed by the UT Dallas team is its unique formulation using dynamic covalent chemistry. Unlike traditional thermoset foams, which undergo irreversible structural changes upon molding and cannot be recycled, the new foam features reversible chemical bonds. These bonds enable the foam to self-repair when damaged, significantly extending its lifespan and usability in various applications, including protective gear like helmets and cushioning in vehicles.
The researchers’ commitment to sustainability cannot be overstated. With rising concerns about environmental pollution due to non-recyclable plastics, the ability to develop a 3D printable foam that can be repaired and potentially recycled positions this research at the forefront of green technology innovation. The team, driven by a dedication to improve the material’s sustainability, has made a conscious effort to explore additional ways to enhance the foam’s recyclability.
As the study unfolds, both Johnson and fellow co-lead author Ariel Tolfree see opportunities for future research that could build on these initial findings. Their curiosity extends beyond simply creating a durable product; it includes questions surrounding how to optimize the material’s properties to accommodate a broader range of applications. This proactive mindset could lead to real-world implementations that not only redefine manufacturing techniques but also significantly impact consumer practices regarding material use and disposal.
In addition to the scientific achievements, the playful element of their tests—a balloon dog—symbolizes the transformation of an ordinary material into something extraordinary. Tolfree eloquently described the representation of the balloon dog as a reflection of their research: what may initially seem unremarkable can be turned into something remarkable with the right technology and approach.
The study’s co-authors, which include a diverse array of graduate students from different fields, reflect the interdisciplinary nature of this research. Bringing together expertise from chemistry and mechanical engineering, the team illustrates the collaborative spirit necessary for advancing complex scientific initiatives. Their diverse educational backgrounds contribute to a comprehensive understanding of both the theoretical and practical challenges in material science.
Funding from prominent institutions, including The Welch Foundation and the National Science Foundation, highlights the significance of this research in the broader scientific community. By investing in such innovative projects, these organizations encourage exploration that fosters advancement in multiple disciplines including chemistry, engineering, and environmental science. Their contributions not only aid the current research but also set the stage for future endeavors that seek to create sustainable solutions for global challenges.
Anticipation surrounds the next steps of this project, as the researchers aim to verify the performance of their foam in real-world applications. Each iteration and experimentation will challenge their initial findings but also potentially yield improvements that refine the material’s capabilities. The road ahead will determine not only the viability of this 3D-printed foam but also its ability to foster advancements in environmentally responsible technologies.
As the researchers publish their findings, they aren’t just sharing knowledge with the scientific community—they’re initiating a dialogue on sustainability, innovation, and the future of materials science. With their pioneering spirit and dedication to merging chemistry with practical applications, they exemplify how research can lead to transformative products tailored to meet modern challenges.
The implications of this research extend far beyond academia; they resonate with consumers who seek products that are not only effective but also environmentally conscious. As awareness grows about the importance of sustainability, the potential for widespread adoption of such innovative materials rises. The researchers at UT Dallas are not just crafting a product; they are paving the way for a new generation of materials that honor both performance and the planet.
In conclusion, the collaboration between chemistry and technology at The University of Texas at Dallas signifies a pivotal moment in efficient material development. Their ongoing commitment to explore various facets of polymer chemistry and 3D printing establishes them as leaders in the quest for sustainable solutions that resonate throughout multiple industries globally.
Subject of Research: 3D-printed foam materials and their properties
Article Title: 3D printable polymer foams with tunable expansion and mechanical properties enabled by catalyst-free dynamic covalent chemistry
News Publication Date: 1-Mar-2025
Web References: RSC Applied Polymers
References: 10.1039/D4LP00374H
Image Credits: University of Texas at Dallas
Keywords
3D printing, polymer foam, dynamic covalent chemistry, sustainability, materials science, recyclability
Tags: 3D-printed foam technologyadvancements in chemistry and technologychallenges in polymer formulationcustom designs in 3D printingdurable foam applicationsenvironmentally friendly polymer foamsflexibility of 3D printingfuture of foam manufacturinginnovative materials science researchrecyclability of 3D-printed materialsRSC Applied Polymers publicationUniversity of Texas at Dallas research
What's Your Reaction?
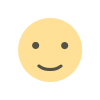
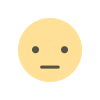
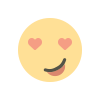
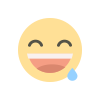
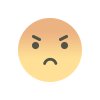
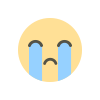
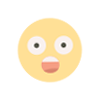