Pioneering diamond manufacturing: Enhancing efficiency and precision with energy beam-based direct and assisted polishing techniques
With the rapid development of semiconductor technologies, diamond emerges as a leading contender in reshaping the modern industry with its remarkable properties. However, the machining of diamond material is very difficult. The polishing technology of diamond, which was used as the jewelry, has developed for hundreds of years. For industrial applications, the mechanical polishing, dynamic […]

With the rapid development of semiconductor technologies, diamond emerges as a leading contender in reshaping the modern industry with its remarkable properties. However, the machining of diamond material is very difficult. The polishing technology of diamond, which was used as the jewelry, has developed for hundreds of years. For industrial applications, the mechanical polishing, dynamic friction polishing, and chemical mechanical polishing were developed for diamond polishing. However, the above polishing methods can cause damage of the surface, such as scratches, cracks, and subsurface damage, which limits the use of diamond substrates in semiconductor and precision optics applications.
Credit: By Zhuo Li, Feng Jiang, Zhengyi Jiang, Zige Tian, Tian Qiu, Tao Zhang, Qiuling Wen, Xizhao Lu, Jing Lu and Hui Huang.
With the rapid development of semiconductor technologies, diamond emerges as a leading contender in reshaping the modern industry with its remarkable properties. However, the machining of diamond material is very difficult. The polishing technology of diamond, which was used as the jewelry, has developed for hundreds of years. For industrial applications, the mechanical polishing, dynamic friction polishing, and chemical mechanical polishing were developed for diamond polishing. However, the above polishing methods can cause damage of the surface, such as scratches, cracks, and subsurface damage, which limits the use of diamond substrates in semiconductor and precision optics applications.
The introduction of energy field to the machining of diamond is a good idea. Energy beam-based polishing technologies utilize lasers, ion beams, or plasma to ablate, impact, or modify the diamond surface. Energy beam-based polishing technologies consist of direct and assisted energy beam-based polishing technologies. Energy beam-based direct polishing technologies include laser polishing and ion beam polishing. Energy beam-based assisted polishing technologies include plasma-assisted polishing and laser-assisted polishing. These technologies have high polishing accuracy and efficiency, which can promote the widespread application of diamonds in modern industrial fields.
To deepen insights into the comprehensive exploration of diamond polishing techniques with enhanced efficiency and precision, researchers from Huaqiao University analyzed the difficulties of the polishing technology for diamonds, summarized the characteristics and future development directions of energy beam direct and assisted polishing technology for diamonds. They summarized four latest polishing technologies, including laser polishing, ion beam polishing, plasma-assisted polishing, and laser-assisted polishing. Material removal mechanisms and influencing factors of the above four latest polishing technologies were analyzed.
This review, published in International Journal of Extreme Manufacturing, systematically summarizes various energy beam-based direct and assisted polishing techniques for diamonds, such as laser polishing, ion beam polishing, plasma assisted polishing, and laser assisted polishing. It analyzes the current research progress, material removal mechanisms, and influencing factors of each polishing technology.
Laser polishing is a non-contact polishing technique that utilizes thermal ablation to graphitize the surface of diamonds, selectively removing protrusions from the diamond surface based on the height difference between surface peaks and valleys. Laser polishing integrates the advantages of laser processing to achieve efficient polishing, but it can easily cause thermal defects on the diamond surface.
Recent studies have mainly focused on improving the polishing quality by selecting reasonable lasers and adjusting laser parameters and incidence angle. Ion beam polishing uses high-energy ion beams or clusters to bombard the surface of diamond substrate or film to remove protrusions by graphitization and amorphization. The type and parameters of ion beams can affect the polishing quality of ion beam polishing.
Plasma assisted polishing is a polishing method combining chemical and mechanical material removal, which involves surface chemical reactions induced by plasma. This method not only obtains high-quality surface but also provides high polishing efficiency. Plasma assisted polishing has been applied to superhard materials such as diamond, sapphire, and silicon carbide. Laser assisted polishing, which is based on laser-induced chemical reactions, has been successfully applied for the polishing of single crystalline diamond, polycrystalline diamond, and diamond films. The main influencing factors of plasma assisted polishing and laser assisted polishing are the type of plasma or laser, type of reactive gas, material of the polishing disc, and the contact parameters of the polishing interface.
Presently, the surface roughness obtained by laser polishing is very limited. The material removal rate of ion beam polishing is low, and the mechanical impact of the ion beam can easily damage the diamond surface. Although both plasma assisted polishing and laser assisted polishing have extremely high polishing accuracy, their material removal rate is limited. In addition, the high equipment cost is still an important factor restricting the application of plasma assisted polishing and laser assisted polishing in the diamond polishing field.
“It is crucial to improve the surface quality of laser polished diamond by selecting a reasonable laser type or adjusting the laser and processing parameters. Improving the material removal rate and reducing the surface damage of ion beam polishing by optimizing the parameters and incidence angle of ion beams should be given considerable attention. In the future, obtaining high-quality diamond surface by using radioactive ion beam, focus ion beam, inductively coupled plasma, or electron cyclotron resonance plasma treatment is an important research direction in the field of ion beam polishing. The material removal rate of plasma assisted polishing and laser assisted polishing can be effectively improved by changing the type of reaction gas and increasing the oxidation rate of the diamond surface. Additionally, reducing the cost by improving the equipment structure can be of great practical significance.” said Professor Jiang.
“Laser polishing has high material removal rate, while ion beam polishing, plasma assisted polishing, and laser assisted polishing have high polishing accuracy. The combination of laser polishing with ion beam polishing, plasma assisted polishing or laser assisted polishing to develop more efficient and high-quality polishing techniques is of immense significance for the high-precision machining of diamonds.”
About IJEM:
International Journal of Extreme Manufacturing (IF: 14.7, 1st in the Engineering, Manufacturing category in JCR 2023) is a new multidisciplinary, double-anonymous peer-reviewed and diamond open-access without article processing charge journal uniquely covering the full spectrum of extreme manufacturing.
The journal is devoted to publishing original articles and reviews of the highest quality and impact in the areas related to the science and technology of manufacturing functional devices and systems with extreme dimensions (extremely large or small) and/or extreme functionalities, ranging from fundamental science to cutting-edge technologies that support the manufacturing of high-performance products involving emerging techniques and breaking the limits of currently known theories, methods, scales, environments, and performance.
Visit our webpage, Like us on Facebook, and follow us on Twitter and LinkedIn.
Journal
International Journal of Extreme Manufacturing
DOI
10.1088/2631-7990/acfd67
Article Title
Energy beam-based direct and assisted polishing techniques for diamond: A review
Article Publication Date
10-Oct-2023
What's Your Reaction?
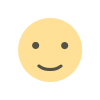
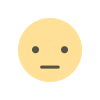
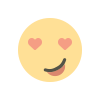
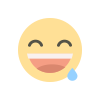
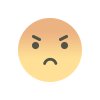
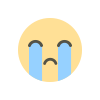
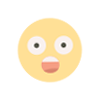