Open-Source 3D Printed Robot Paves the Way for Accessible Materials Synthesis
In an era where automation is pivotal in advancing research, a team from Hokkaido University is leading the charge with the development of FLUID (Flowing Liquid Utilizing Interactive Device), an innovative, open-source robotic system designed for material synthesis. This cutting-edge advancement not only reflects a significant leap in robotics but also embodies the philosophy of […]

In an era where automation is pivotal in advancing research, a team from Hokkaido University is leading the charge with the development of FLUID (Flowing Liquid Utilizing Interactive Device), an innovative, open-source robotic system designed for material synthesis. This cutting-edge advancement not only reflects a significant leap in robotics but also embodies the philosophy of accessibility in scientific equipment. By integrating 3D printing and off-the-shelf electronic components into its design, the researchers have effectively democratized the capabilities traditionally reserved for high-budget laboratories, presenting a solution that could revolutionize how experiments are conducted across various fields in materials science.
The research led by Professor Keisuke Takahashi has opened new avenues for scientists who seek to explore automated experimentation without the heavy financial burden usually associated with commercial robotic systems. The FLUID robot is ingeniously designed, utilizing four independent modules, each of which is methodically equipped with a syringe, two valves, and precise control mechanisms that include servo and stepper motors. Not only do these components facilitate accurate material synthesis, but they also empower researchers to tailor the robot to their specific experimental needs without the typical constraints imposed by proprietary systems.
One of the standout features of the FLUID system is its remarkable ability to automate complex processes like the co-precipitation of cobalt and nickel, producing binary materials with a level of precision that was previously labor-intensive and time-consuming. This operational efficiency is enhanced by the robot’s integration of user-friendly software that allows operators to manage valve configurations, syringe movements, and real-time monitoring of experimental conditions directly from their computers. Such technology merges functionality with ease of use, ensuring that scientists can focus on experiments rather than the intricacies of robotic operation.
A key advantage of FLUID is its open-source nature, which means that the design files are readily available for researchers worldwide to modify and replicate. This approach not only fosters collaboration within the global research community but also significantly lowers the barrier to entry for institutions and laboratories that may lack the financial resources for high-end equipment. The democratization of technology in this manner is vital for promoting equitable scientific progress, particularly in resource-limited environments where such innovations can catalyze significant advancements in research capabilities.
The technical design of the robot showcases a high level of ingenuity, incorporating essential elements like end-stop sensors that detect the syringe’s filling position, ensuring operational safety and precision. Each module can operate independently, yet they are seamlessly integrated into a cohesive system controlled via a microcontroller. This advanced architecture underlines the adaptability of FLUID, making it suitable for a wider variety of chemical processes beyond just material synthesis, thereby expanding the potential applications of this technology further into the realm of automation in scientific research.
Looking to the future, the researchers are setting their sights on enhancing FLUID’s capabilities even further. Plans include the integration of additional sensors aimed at monitoring various parameters such as temperature and pH levels, which will significantly broaden the scope of chemical reactions that can be efficiently managed by this robotic system. This development highlights an important aspect of innovation—the need for continuous evolution and adaptation based on user feedback and emerging scientific requirements.
Moreover, improving the accompanying software to include features like macro recording is high on the agenda. This will facilitate the automation of repetitive tasks, drastically reducing the time scientists spend on experimental procedures. Enhanced data logging capabilities will further refine the experimental reproducibility and analysis, ensuring that results are not only consistent but also easily interpretable. Such advancements would not only streamline workflow but would also enhance the quality and reliability of scientific findings.
The open-source model of FLUID aligns with a broader trend in the scientific community that advocates for transparency and collaboration. Researchers are increasingly recognizing that sharing technological advancements can lead to quicker innovations and improvements in the field. By fostering an environment where ideas are exchanged freely, the scientific world can tackle complex challenges more efficiently than ever before. It is a powerful reminder that collaboration, rather than competition, is often the key to significant breakthroughs.
As scientists around the globe engage with FLUID, they will no doubt contribute to its ongoing development, suggesting modifications and enhancements that reflect the diverse needs of various research disciplines. As more researchers utilize this platform, it will undoubtedly yield a wealth of data that can inform further research and development in automation and material science.
In conclusion, FLUID represents a landmark achievement in the field of robotic automation for materials synthesis. Through its innovative design, affordability, and open-source accessibility, it promises to reshape the landscape of scientific research, enabling a more inclusive and efficient approach to discovery. Professor Takahashi and his team have set a benchmark, not just in the functionality of their device, but in the ethos of scientific inquiry itself—an ethos that champions collaboration, openness, and the relentless pursuit of knowledge. This revolutionary step toward democratizing technology in research embodies the future of science—where every innovation is available to those willing to explore its potential.
Subject of Research: Not applicable
Article Title: Development of an Open-Source 3D-Printed Material Synthesis Robot FLUID: Hardware and Software Blueprints for Accessible Automation in Materials Science
News Publication Date: 9-Apr-2025
Web References:
References:
Image Credits: Credit: Keisuke Takahashi
Keywords
Automation, Robotics, Open-Source Technology, Material Synthesis, Science Innovation, 3D Printing, Research Accessibility, Experimental Design, Hokkaido University, Scientific Collaboration.
Tags: 3D printed automationaccessible scientific equipmentadvancements in materials scienceautomated experimentation in sciencecost-effective laboratory solutionscustomizable experimental setupsdemocratization of research toolsHokkaido University researchinnovative robotic systemsmaterial synthesis technologymodular robotic designopen-source robotics
What's Your Reaction?
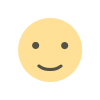
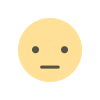
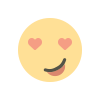
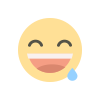
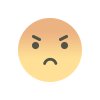
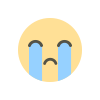
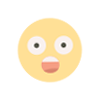