New biodegradable plastics are compostable in your backyard
We use plastics in almost every aspect of our lives. These materials are cheap to make and incredibly stable. The problem comes when we’re done using something plastic — it can persist in the environment for years. Over time, plastic will break down into smaller fragments, called microplastics, that can pose significant environmental and health […]

We use plastics in almost every aspect of our lives. These materials are cheap to make and incredibly stable. The problem comes when we’re done using something plastic — it can persist in the environment for years. Over time, plastic will break down into smaller fragments, called microplastics, that can pose significant environmental and health concerns.
Credit: Mark Stone/University of Washington
We use plastics in almost every aspect of our lives. These materials are cheap to make and incredibly stable. The problem comes when we’re done using something plastic — it can persist in the environment for years. Over time, plastic will break down into smaller fragments, called microplastics, that can pose significant environmental and health concerns.
The best-case solution would be to use bio-based plastics that biodegrade instead, but many of those bioplastics are not designed to degrade in backyard composting conditions. They must be processed in commercial composting facilities, which are not accessible in all regions of the country.
A team led by researchers at the University of Washington has developed new bioplastics that degrade on the same timescale as a banana peel in a backyard compost bin. These bioplastics are made entirely from powdered blue-green cyanobacteria cells, otherwise known as spirulina. The team used heat and pressure to form the spirulina powder into various shapes, the same processing technique used to create conventional plastics. The UW team’s bioplastics have mechanical properties that are comparable to single-use, petroleum-derived plastics.
The team published these findings June 20 in Advanced Functional Materials.
“We were motivated to create bioplastics that are both bio-derived and biodegradable in our backyards, while also being processable, scalable and recyclable,” said senior author Eleftheria Roumeli, UW assistant professor of materials science and engineering. “The bioplastics we have developed, using only spirulina, not only have a degradation profile similar to organic waste, but also are on average 10 times stronger and stiffer than previously reported spirulina bioplastics. These properties open up new possibilities for the practical application of spirulina-based plastics in various industries, including disposable food packaging or household plastics, such as bottles or trays.”
The researchers opted to use spirulina to make their bioplastics for a few reasons. First of all, it can be cultivated on large scales because people already use it for various foods and cosmetics. Also, spirulina cells sequester carbon dioxide as they grow, making this biomass a carbon-neutral, or potentially carbon-negative, feedstock for plastics.
“Spirulina also has unique fire-resistant properties,” said lead author Hareesh Iyer, a UW materials science and engineering doctoral student. “When exposed to fire, it instantly self-extinguishes, unlike many traditional plastics that either combust or melt. This fire-resistant characteristic makes spirulina-based plastics advantageous for applications where traditional plastics may not be suitable due to their flammability. One example could be plastic racks in data centers because the systems that are used to keep the servers cool can get very hot.”
Creating plastic products often involves a process that uses heat and pressure to shape the plastic into a desired shape. The UW team took a similar approach with their bioplastics.
“This means that we would not have to redesign manufacturing lines from scratch if we wanted to use our materials at industrial scales,” Roumeli said. “We’ve removed one of the common barriers between the lab and scaling up to meet industrial demand. For example, many bioplastics are made from molecules that are extracted from biomass, such as seaweed, and mixed with performance modifiers before being cast into films. This process requires the materials to be in the form of a solution prior to casting, and this is not scalable.”
Other researchers have used spirulina to create bioplastics, but the UW researchers’ bioplastics are much stronger and stiffer than previous attempts. The UW team optimized microstructure and bonding within these bioplastics by altering their processing conditions — such as temperature, pressure, and time in the extruder or hot-press — and studying the resulting materials’ structural properties, including their strength, stiffness and toughness.
These bioplastics are not quite ready to be scaled up for industrial usage. For example, while these materials are strong, they are still fairly brittle. Another challenge is that they are sensitive to water.
“You wouldn’t want these materials to get rained on,” Iyer said.
The team is addressing these issues and continuing to study the fundamental principles that dictate how these materials behave. The researchers hope to design for different situations, by creating an assortment of bioplastics. This would be similar to the variety of existing petroleum-based plastics.
The newly developed materials are also recyclable.
“Biodegradation is not our preferred end-of-life scenario,” Roumeli said. “Our spirulina bioplastics are recyclable through mechanical recycling, which is very accessible. People don’t often recycle plastics, however, so it’s an added bonus that our bioplastics do degrade quickly in the environment.”
Co-authors on this paper are UW materials science and engineering doctoral students Ian Campbell and Mallory Parker; Paul Grandgeorge, a UW postdoctoral scholar in materials science and engineering; Andrew Jimenez, who completed this work as a UW postdoctoral scholar in materials science and engineering and is now at Intel; Michael Holden, a UW master’s student studying materials science and engineering; Mathangi Venkatesh, a UW undergraduate student studying chemical engineering; Marissa Nelsen, who completed this work as a UW undergraduate student studying biology; and Bichlien Nguyen, a principal researcher at Microsoft. This research was funded by Microsoft, Meta and the National Science Foundation.
###
For more information, contact Roumeli at eroumeli@uw.edu. Note: Roumeli is on Eastern Time this week.
Journal
Advanced Functional Materials
DOI
10.1002/adfm.202302067
Article Title
Fabricating Strong and Stiff Bioplastics from Whole Spirulina Cells
Article Publication Date
20-Jun-2023
What's Your Reaction?
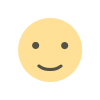
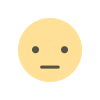
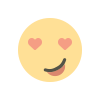
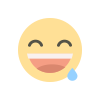
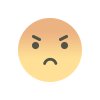
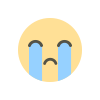
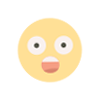