MIT Engineers Develop Printable Synthetic Metamaterials Combining Strength and Stretchability
In a breakthrough that challenges long-held material science paradigms, engineers at the Massachusetts Institute of Technology have developed a novel metamaterial that seamlessly combines strength with extraordinary stretchability. Traditionally, materials have faced an intrinsic compromise: hardness and rigidity come at the expense of flexibility, rendering strong materials brittle and prone to fracture. However, this new […]

In a breakthrough that challenges long-held material science paradigms, engineers at the Massachusetts Institute of Technology have developed a novel metamaterial that seamlessly combines strength with extraordinary stretchability. Traditionally, materials have faced an intrinsic compromise: hardness and rigidity come at the expense of flexibility, rendering strong materials brittle and prone to fracture. However, this new innovation in metamaterial design opens up possibilities for creating materials that are not only robust but also capable of sustaining substantial deformation without failure.
Metamaterials are engineered structures with microscopic architectures that endow them with properties unattainable by natural substances. For years, the pursuit within this field has focused on maximizing stiffness and strength, often overlooking the potential benefits of incorporating flexibility into these exotic materials. MIT’s latest research overturns this tradition by demonstrating how the interplay of two distinct microscopic networks — a rigid scaffold combined with a soft woven weave — can produce an overall material that excels in both mechanical toughness and elasticity.
At the heart of the discovery lies a double-network configuration realized using two-photon lithography, a cutting-edge laser-based 3D printing method capable of fabricating structures at the microscale with astonishing precision. The first network comprises stiff, grid-like struts and trusses fabricated from an acrylic polymer similar to plexiglass, known for its brittleness. Intertwined with this is a second network formed by soft, coil-shaped springs that weave intricately around the rigid framework. This combination, inspired by the molecular architecture of tough hydrogels, imparts the resulting metamaterial with a resilience and elasticity previously thought impossible for such stiff base materials.
The double-network approach mimics principles observed in hydrogels—soft, water-rich substances that exhibit both stretch and toughness by combining a rigid polymer network chemically intertwined with a soft polymer matrix. MIT’s engineers translated this molecular motif into a microscale mechanical system, leveraging the strengths of each component. The rigid lattice sustains loads and maintains structural integrity, while the flexible coil network dissipates energy and accommodates deformation through entanglement and friction.
Experimental testing revealed that this interconnected architecture could stretch to over four times its original length without catastrophic failure. This remarkable stretchability starkly contrasts the behavior of the base polymer when structured conventionally, which tends to shatter almost immediately post-crack formation. The team subjected samples, ranging in size from a few square microns to millimeters, to nanomechanical tensile testing, capturing high-resolution observations of crack propagation, deformation modes, and energy dissipation mechanisms.
Intriguingly, the softer coil network acts like a tangle of spaghetti wrapped around the rigid lattice. As fractures initiate in the stiffer network, fragments do not separate cleanly but instead become caught and intertwined within the flexible coils. This entanglement causes stress to spread non-uniformly and halts cracks from progressing linearly, effectively toughening the material and enabling it to absorb significantly more energy. This microstructural synergy between stiff and soft components redefines how mechanical load is managed at the microscale.
Moreover, the researchers discovered that introducing deliberate “defects” or microscopic holes into the metamaterial’s lattice further enhanced its extensibility and toughness. Contrary to conventional wisdom where defects weaken materials, these strategically placed voids act as sites for distributing stress and encouraging more frictional interactions between coil fibers and fractured struts. This finding suggests a new design paradigm in which imperfections can be cleverly employed to optimize functionality rather than compromise performance.
Beyond the remarkable mechanical properties, the potential applications of such double-network metamaterials span a broad spectrum of industries and technologies. The team envisions robust and tear-resistant textiles that can stretch comfortably, flexible semiconductors capable of adapting to bending and deformation, and scaffold materials for tissue engineering that combine durability with compliance to biological movement. This convergence of strength and flexibility could revolutionize fields from wearable electronics to regenerative medicine.
MIT engineers have also established a computational framework capable of predicting material behavior based on the interplay between the stiff and flexible networks. This tool will assist researchers and engineers in tailoring metamaterials to specific mechanical requirements, accelerating the path toward practical, application-ready designs. Such predictive capability is indispensable for integrating these innovative materials into devices where both toughness and adaptability are critical.
The project’s lead, Professor Carlos Portela, articulates an even more ambitious vision: extending this double-network strategy to inherently more brittle materials such as ceramics, glasses, and metals. By adapting the interwoven microarchitecture to these substances, it may become feasible to produce multifunctional materials with tailor-made responses, including thermal sensitivity and conductivity. Imagine fabrics that adjust their rigidity based on ambient temperature or circuits capable of withstanding mechanical stresses without failure.
This research represents a significant leap in materials science, where the manual design of microarchitectures allows for tailored tuning of mechanical responses that transcend the limitations of chemistry alone. The fusion of bio-inspired concepts with advanced additive manufacturing technologies heralds a new interdisciplinary frontier, blending physics, engineering, and chemistry. It opens a pathway toward a new generation of “smart” materials that are simultaneously resilient, flexible, and functional.
Such advances would be impossible without the synergy of high-precision fabrication, sophisticated mechanical testing, and insightful biomimetic inspiration. The team’s work also highlights the importance of revisiting and challenging longstanding assumptions about material properties, especially the belief that stiffness and stretchability cannot coexist. With these double-network metamaterials, MIT engineers have unveiled a brave new realm where materials can be designed by architecture as much as by composition.
As metamaterials continue to evolve, the implications for technological innovation are profound. From aerospace components that must endure extreme conditions to biomedical implants requiring both durability and compliance, the marriage of strength and elasticity may redefine material capabilities across many scientific domains. The double-network concept thus stands as a landmark accomplishment, signaling a future where the limits of material performance are set not by nature but by human ingenuity.
This pioneering research, soon to be published in Nature Materials, represents a meaningful step forward in the quest for advanced materials. Supported by the U.S. National Science Foundation and the MIT MechE MathWorks Seed Fund, this study underscores the collaborative power of engineering disciplines and offers an exciting glimpse into the transformative potential of metamaterial science.
Subject of Research: Development of double-network-inspired mechanical metamaterials combining stiffness and stretchability.
Article Title: “Double-network-inspired mechanical metamaterials”
Image Credits: Courtesy of Carlos Portela, et al
Keywords
Metamaterials, Printing, Textile engineering, Tissue structure, Mechanical stress, Chemical engineering, Computer science, Mechanical engineering, Ceramics, Conductive polymers, Synthetic polymers, Metals, Chemical structure, Polymer architecture, Mechanical energy, Hydrogels, Glass, Electronics, Semiconductors
Tags: advanced 3D printing techniquesdouble-network configuration in materialsengineered materials with unique propertiesinnovative material science breakthroughsmechanical toughness and elasticitymetamaterials for flexible applicationsMIT synthetic metamaterialsovercoming rigidity in material designprintable metamaterials technologyrobust materials with deformation capabilitiesstrength and stretchability in materialstwo-photon lithography applications
What's Your Reaction?
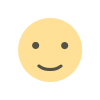
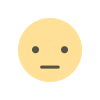
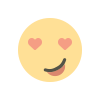
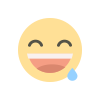
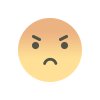
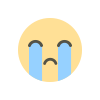
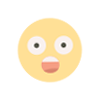