Fission chips – How vinegar could revolutionize sensor processing
Researchers at Macquarie University have developed a new way to produce ultraviolet (UV) light sensors, which could lead to more efficient and flexible wearable devices. Credit: Huang and Nasiri Researchers at Macquarie University have developed a new way to produce ultraviolet (UV) light sensors, which could lead to more efficient and flexible wearable devices. The […]

Researchers at Macquarie University have developed a new way to produce ultraviolet (UV) light sensors, which could lead to more efficient and flexible wearable devices.
Credit: Huang and Nasiri
Researchers at Macquarie University have developed a new way to produce ultraviolet (UV) light sensors, which could lead to more efficient and flexible wearable devices.
The study, published in the journal Small in July, shows how acetic acid vapour – essentially vinegar fumes – can rapidly improve the performance of zinc oxide nanoparticle-based sensors without using high-temperatures for processing.
Co-author Professor Shujuan Huang, from the School of Engineering at Macquarie University, says: “We found by briefly exposing the sensor to vinegar vapour, adjoining particles of zinc oxide on the sensor’s surface would merge together, forming a bridge that could conduct energy.”
Joining zinc oxide nanoparticles together is a critical part of building tiny sensors, as it creates channels for electrons to flow through.
The research team found that their vapour method could make UV detectors 128,000 more responsive than untreated ones, and the sensors could still accurately detect UV light without interference, making them highly sensitive and reliable.
Associate Professor Noushin Nasiri, co-author on the paper and head of the Nanotech Laboratory at Macquarie University, says: “Usually, these sensors are processed in an oven, heated at high temperature for 12 hours or so, before they can operate or transmit any signal.”
But instead, the team found a simple chemical way to copy the effects of the heat process.
“We found a way to process these sensors at room temperature with a very cheap ingredient – vinegar. You just expose the sensor to vinegar vapour for five minutes, and that’s it – you have a working sensor,” she says.
To create the sensors, the researchers sprayed a zinc solution into a flame, producing a fine mist of zinc oxide nanoparticles that settled onto platinum electrodes.
This formed a thin sponge-like film, which they then exposed to vinegar vapour for five to 20 minutes.
The vinegar vapour changed how the tiny particles in the film were arranged, helping the particles connect to each other, so electrons could flow through the sensor. At the same time, the particles stayed small enough to detect light effectively.
“These sensors are made of many, many tiny particles that need to be connected for the sensor to work,” says Associate Professor Nasiri.
“Until we treat them, the particles just sit next to each other, almost as if they have a wall around them, so when light creates an electrical signal in one particle, it can’t easily travel to the next particle. That’s why an untreated sensor doesn’t give us a good signal.”
The researchers went through intensive testing of different formulations before hitting on the perfect balance in their process.
“Water alone isn’t strong enough to make the particles join. But pure vinegar is too strong and destroys the whole structure,” says Professor Huang. “We had to find just the right mix.”
The study shows the best results came from sensors exposed to the vapour for around 15 minutes. Longer exposure times caused too many structural changes and worse performance.
“The unique structure of these highly porous nanofilms enables oxygen to penetrate deeply, so that the entire film is part of the sensing mechanism,” Professor Huang says.
The new room-temperature vapour technique has many advantages over current high-temperature methods. It allows the use of heat-sensitive materials and flexible bases, and is cheaper and better for the environment.
Associate Professor Nasiri says the process can easily be scaled up commercially.
“The sensor materials could be laid out on a rolling plate, passing through an enclosed environment with vinegar vapours, and be ready to use in less than 20 minutes.”
The process will be a real advantage in creating wearable UV sensors, which need to be flexible and to use very little power.
Associate Professor Nasiri says that this method for UV sensors could be used for other types of sensors too, using simple chemical vapour treatments instead of high-temperature sensor processing across a wide range of functional materials, nanostructures and bases or substrates.
Journal
Small
DOI
10.1002/smll.202402558
Method of Research
Experimental study
Subject of Research
Not applicable
Article Title
Vapor-Tailored Nanojunctions in Ultraporous ZnO Nanoparticle Networks for Superior UV Photodetection
Article Publication Date
20-Jul-2024
COI Statement
The authors declare no conflicts.
What's Your Reaction?
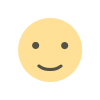
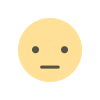
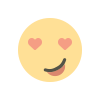
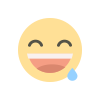
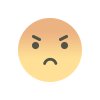
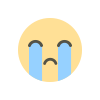
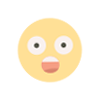