Ammonia-free gallium nitride semiconductor production improves crystal quality and reduces environmental impact
Gallium nitride (GaN) semiconductors can now be grown without ammonia, a toxic chemical that needs a sophisticated detoxifying system before it can be released into the atmosphere. The new technique is not only more environmentally friendly but also allows for the efficient and high-quality growth of crystals at a lower cost. Scientists can make semiconductors […]

Gallium nitride (GaN) semiconductors can now be grown without ammonia, a toxic chemical that needs a sophisticated detoxifying system before it can be released into the atmosphere. The new technique is not only more environmentally friendly but also allows for the efficient and high-quality growth of crystals at a lower cost. Scientists can make semiconductors more efficiently with a reduced need for raw materials and power. Researchers from Nagoya University in Japan led the study, which was published in Scientific Reports.
Credit: Reiko Matsushita
Gallium nitride (GaN) semiconductors can now be grown without ammonia, a toxic chemical that needs a sophisticated detoxifying system before it can be released into the atmosphere. The new technique is not only more environmentally friendly but also allows for the efficient and high-quality growth of crystals at a lower cost. Scientists can make semiconductors more efficiently with a reduced need for raw materials and power. Researchers from Nagoya University in Japan led the study, which was published in Scientific Reports.
GaN is a compound made up of gallium (Ga) and nitrogen (N) that acts as a semiconductor. GaN semiconductors are extensively used in mobile base stations, fast charging power supply adapters, microwave and millimeter wave communications, imaging, radio astronomy, power switching, and radar systems, including military systems, because of their ability to handle high voltage and current.
The most used technique for commercial production of GaN films is metal organic chemical vapour deposition (MOCVD), which uses ammonia (NH3) gas as the source of nitrogen added to the Ga. However, the rate at which ammonia is broken up in this process, known as the decomposition efficiency, is very low.
“As a result, a large consumption of ammonia is necessary,” said corresponding researcher Arun Dhasiyan. “Ammonia is a very toxic and corrosive gas if inhaled that can cause severe damage to the eyes, skin, and respiratory system. Because it is so toxic, much of the ammonia has to be detoxicated and disposed of unused, requiring a lot of energy. This is a large part, up to half, of the total production cost.”
To produce activated nitrogen, the group led by Professors Masaru Hori and Kenji Ishikawa with Dr. Dhasiyan of Nagoya University’s cLPS department activated nitrogen, a readily available gas in the atmosphere, by applying very high-frequency power (100 MHz) to one of the electrodes.
Using this patented technique, the team developed low-cost, high-quality GaN material for semiconductor devices. “Our method, known as the REMOCVD method, solves three problems of GaN growth,” Dhasiyan explained. “It enables the growth of GaN semiconductors at lower temperatures (about 800°C compared to over 1150°C); it uses nitrogen and hydrogen gas instead of ammonia gas, saving on raw materials and lowering the production cost; and also cuts out the extraction of nitrogen from ammonia step, making the process faster at lower temperatures.”
Their new crystal growth method stands to replace the conventional method, as it is easy to industrialize and produces GaN semiconductors with less impurities. The team expects the development of new technology to enhance low-power-consumption GaN semiconductor devices, resulting in more efficient power devices.
Presently, industrial equipment for large-diameter substrates of 150-300 mm is required for applications to power devices and low-cost LEDs. The group installed a 300-mm diameter REMOCVD system to test the large-scale production. They are convinced that the high growth rate and crystal quality of GaN using REMOCVD will soon replace the MOCVD method.
“At cLPS, we have grown GaN, aluminum nitride, indium nitride, and aluminum indium nitride layers using the REMOCVD method and found that it is very effective to grow all of these commonly used semi-conductor materials at much lower temperatures than those of the MOCVD method without using any ammonia gas,” said Dhasiyan. “The most exciting thing is that the crystal quality and the growth speed are close to that of MOCVD, so we can enjoy the same level of quality with less environmental impact.”
About cLPS
The Center for Low-temperature Plasma Sciences, or cLPS, is located at Nagoya University. Its goal is to support sustainable development for all by pushing the boundaries of interdisciplinary fields to foster innovation in plasma science research and development. The future of industries and the global environment lies in plasma science.
Journal
Scientific Reports
DOI
10.1038/s41598-024-61501-9
What's Your Reaction?
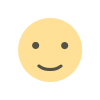
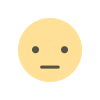
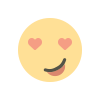
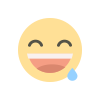
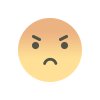
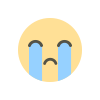
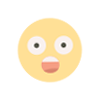