A Space: Science & Technology study advances numerical research for optimizing micronozzle performance
The micronozzle, which is a core component of the electrothermal microthruster, features a micron-scale geometry, a 2D Laval configuration, a rectangular cross section, and a highly thermal conductive silicon wall due to MEMS fabrication. As a result, viscous loss in the flow field and heat transfer to the nozzle wall can strongly influence nozzle performance, […]

The micronozzle, which is a core component of the electrothermal microthruster, features a micron-scale geometry, a 2D Laval configuration, a rectangular cross section, and a highly thermal conductive silicon wall due to MEMS fabrication. As a result, viscous loss in the flow field and heat transfer to the nozzle wall can strongly influence nozzle performance, namely, thrust force and specific impulse. In the new paper published in the journal Space: Science & Technology, Xiaoqian Chen, Xingchen Li et al. report a numerical research on MEMS (microelectromechanical system) micronozzles through multiphysics coupling simulation along with design optimization based on simulation results.
Credit: Space: Science & Technology
The micronozzle, which is a core component of the electrothermal microthruster, features a micron-scale geometry, a 2D Laval configuration, a rectangular cross section, and a highly thermal conductive silicon wall due to MEMS fabrication. As a result, viscous loss in the flow field and heat transfer to the nozzle wall can strongly influence nozzle performance, namely, thrust force and specific impulse. In the new paper published in the journal Space: Science & Technology, Xiaoqian Chen, Xingchen Li et al. report a numerical research on MEMS (microelectromechanical system) micronozzles through multiphysics coupling simulation along with design optimization based on simulation results.
Being identical to the prototype MEMS thruster, the simulated micronozzle consists of 3 geometrical parts, namely, the upper covering layer, the substrate, and the micronozzle itself. The upper covering layer is defined with properties of a Pyrex glass and substrate with properties of silicon (Fig.3). To better understand thermodynamic interaction between gas flow and micronozzle wall, numerical simulation coupling of flow dynamics field and solid heat transfer field is adopted.
1. Effect of wall heat transfer
A prototype micronozzle is tested in both thermal conductive and adiabatic status to reveal the effect of wall heat transfer on nozzle performance. The wall heat transfer leads to 2 results. The first is the loss of flow energy with reduction of specific impulse. The second is the increasing mass flow rate due to temperature reduction in parallel and converging ducts. Furthermore, a quantitative analysis is conducted by comparing nozzle performance of 2 kinds in Table 3. As calculated, wall heat transfer leads to a 13.1% loss of specific impulse and a 19.2% increase of mass flow rate. In total, the thrust is increased by 4.8% under the combined effect.
2. Design optimization for linear micronozzle
2.1 Convergence duct design optimization
A direct-turning side wall can lead to performance loss because of flow stagnation at the corner (Fig.14). To eliminate the corner vortex, a rounded corner with a radius of 400 μm is built to connect the side wall of the parallel duct and tje convergence duct. The thrust grows and specific impulse diminishes with large half convergence angle, which is a trend generally independent of the half divergence angle. For a larger convergence angle, rounded turning shows a greater improvement in specific impulse (Fig.15).
2.2 Throat design optimization
The traditional nozzle geometry features a side wall with sharp turning, and this design leads to different degrees of flow separation according to different turning angles. A curved-turning throat is able to let working fluid move close to the side wall and turn off smoothly.
Fig.16 offers a comparison between flow in micronozzle with and without the curved-turning throat when all other geometry parameters are kept identical.
Fig. 17 and 18 show how nozzle performance changes as a function of half divergence angle and radius of curvature at the throat. Half convergence angle is defined as 60° in geometry. The throat design shows a strong influence on thrust and a slight influence on specific impulse, but both thrust and specific impulse show a similar trend to the radius of curvature. Nozzles with a throat radius of 160 μm outperform others, increasing thrust by about 3% and specific impulse by 1%.
2.3 Expander design optimization
Fig. 19 shows the relation between nozzle performance and expander structural parameters. Parametric simulation is carried out between half divergence angles of 15° and 30° at intervals of 5° and exit-to-throat ratio between 3 and 10. For larger half divergence angle, an optimum exit-to-throat section ratio increases as a larger half divergence angle allows shorter expander, which leads to smaller viscous loss with the same exit-to-throat ratio.
2.4 Optimum design through CobyLA
According to the analysis above, the half convergence angle can be decided as 60° and radius at throat can be decided as 160 μm for the maximum specific impulse. However, the accurate value of half divergence angle (θdiv) and exit-to-throat section ratio (Rex) should be further studied. Several optimization procedures are conducted with different initial values by CObyLA, and the optimizing process can be demonstrated in Fig. 20. Global convergence of optimum design features Rex of 6.20 and θdiv of 16.9°. As a result, the linear expander micronozzle with Rex of 6.20 and θdiv of 16.9° is believed as the optimum design, which features 7% increase of thrust and 2% increase of specific impulse compared with the prototype micronozzle.
3. Performance of optimum micronozzle
To further cut down non-axial velocity loss at exit, the bell-shaped expander is brought in. The bell-shaped expander is defined, referring a parabolic definition with 3 independent variables, namely, exit-to-throat section ratio (Rex), half divergence angle at throat (θthroat), and relative length (RL)(Fig.21). A flow field comparison is demonstrated between the linear expander optimum micronozzle and the bell-shaped one in Fig. 22. As is shown, non-axial velocity at the exit section is effectively reduced by the bell-shaped contour.
The optimum parameter set is chosen through CObyLA, and the performance of the bell-shaped design is compared with the linear expander design under different throat Reynolds numbers. To the contrary of expectation, the optimum linear expander design outperforms the bell-shaped one on both thrust and specific impulse. This result can be attributed to the turn-back geometry, causing compression waves pointing to the central symmetrical plane. The accumulation of the low-velocity boundary layer near the central symmetrical plane leads to a 2% to 3% larger portion of low velocity flow compared with the linear expander micronozzle. Thus, the linear expander is believed to be the appropriate design for the MEMS micronozzle.
To further validate the performance comparison between the linear expander micronozzle and the bell-shaped one that has been done in this paper through simulation method, experimental measurements will be put forward in the next study step.
Reference
Authors: XINGCHEN LI, HAOPENG LIANG, RUOFAN ZHANG, WEN YAO , AND XIAOQIAN CHEN
Title of the Original Paper: Multiphysics Numerical Simulation and Geometric Optimization of a Micronozzle for the MEMS Thruster
Journal: Space: Science & Technology
Journal
Space: Science & Technology
DOI
10.34133/space.0032
Article Title
Multiphysics Numerical Simulation and Geometric Optimization of a Micronozzle for the MEMS Thruster
Article Publication Date
31-May-2023
What's Your Reaction?
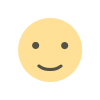
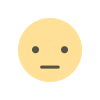
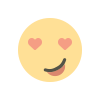
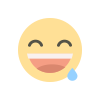
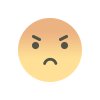
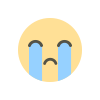
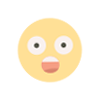